Support for C4-16000 scientific CMOS camera
The first member of the premium C4 series of scientific camera,
the C4-16000 with 4k × 4k resolution
CMOS sensor and 37 × 37 mm sensitive area (geometrically equivalent to
workhorse G4-16000 CCD camera) is now supported in SIPS. While the
sensor used in the C4 cameras uses 12-bit A/D converters only, it
is capable to digitize image twice, and thus allows reading of two
images from single exposure. One image uses high-gain digitization
channel, while the other image is digitized using low-gain
channel. These two images with 12-bit depth are then combined into
single image with true 16-bit dynamic range.
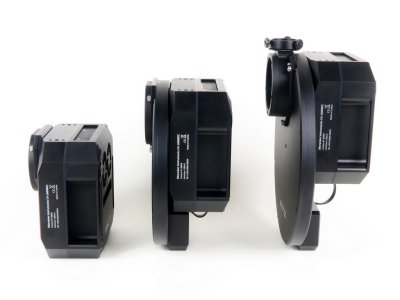
C4-16000 cameras can be combined with various External
filter wheels
Support for hardware sub-frames on Cx CMOS based
cameras
Restriction of image read to a sub-frame (sometimes call
region-of-interest or just ROI) was naturally available in all CCD
based Gx cameras. The CCD is a serial device and reading of a
sub-frame does not reduce the digitization time significantly (all
pixels have to be shifted through the sensor and limiting read to
a sub-frame only saves time for digitization of pixels outside of
the sub-frame). Because digitization of individual pixels is
performed by camera electronics, outside of the CCD sensor,
sub-frame read of a CCD is implemented in the camera and the
sensor itself has little or no influence on this function.
Situation with CMOS sensors is just opposite — reading of a sub-frame has to be implemented in the
sensor hardware/firmware and camera electronics cannot affect it.
So, the question is why sub-frame read of CMOS sensors in Cx
cameras was implemented by software cropping, when the used IMX
sensors support sub-frame (ROI) read? The problem is in ROI
support by sensor hardware — it imposes
number of limitations on the sub-frame position and size. What's
more, these limitations differ among various sensors and also
between 8-bit and 12-bit read modes of the same sensor etc. For
instance, sub-frame origin must be aligned to certain multiply of
pixels (typically 4 or 8 pixels). The same limitation is valid for
sub-frame width and height. Also, minimal sub-frame width is often
several hundred pixels etc.
But SIPS camera drivers as well as user interface were not
designed to impose any sub-frame position/size restrictions.
Inability to do sub-frame read without any limitations lead to
reading of the whole frame from the camera and cropping to (this
time arbitrary) sub-frame by driver. Time penalty when e.g.
12 MPx frames are read and cropped to
300 kPx is obvious, the FPS in such
case was 40-times lower than theoretically possible.
No restrictions on sub-frame position and size design
remained present also in SIPS v3.21. But the new Cx camera driver
combines both approaches — when a sub-frame
read is requested by the user, Cx camera driver checks if the
sub-frame position and size comply to sensor-imposed limitations.
If yes, camera hardware is programmed to limit read to specific
ROI only and resulting image is directly returned to the user. If
the requested sub-frame position and/or size does not fit sensor
limitations, the driver enlarges the sub-frame size and position
to satisfy the sensor and at the same time to be the smallest
possible one, but containing the user requested sub-frame. This
greater sub-frame is then read from camera and cropped by driver
to the size requested by the user. Differences in sub-frame read
from camera and sub-frame returned to the user are typically very
small, a few pixels necessary to align position and size to
multiply of 4 or 8 pixels etc. So, amount of data transferred from
camera is almost the same, only the software cropping consumes
some time.
Hint: Often the user, choosing the sub-frame, has no strict
requirements to its position and size. From the user point of
view, slightly adjusting the sub-frame to fit sensor limitations
is not a problem. And doing so means sub-frame size and position
can be programmed directly to the camera and images returned to
the user without the necessity to perform time-consuming cropping
in software. This is why the Frame tab of the
Imager tool in SIPS v3.21 adds a new button Adjust
Frame. Clicking this button checks if the currently selected
sub-frame fits to sensor limitations. If no, position and size are
adjusted to the smallest possible sub-frame still containing the
originally selected one. Reading of images then can be performed
directly, without software cropping.
Sensor characterization using Photon Transfer
Curve
Laws of physics dictate that the variations of signal acquired
by a sensor (light incoming to camera from a telescope in our
case) are proportional to the square root of signal value. This
law can be used to characterize every solid state detector (both
CCD and CMOS) purely on a series of uniform light images (flat
fields). Even if particular manufacturer does not publish key
sensor parameters like conversion factors in e-/ADU, full well
capacity in e- or absolute read noise in e- RMS, analyzing series
of flat field images covering the sensor dynamic range and
constructing so-called Photon Transfer Curve can reveal them.
SIPS v3.21 adds one new tool button to every image set,
performing the sensor characterization. To work properly, the set
must contain pairs of evenly illuminated images of the same
exposure. No Dark nor Bias frames should be subtracted from these
light images. Exposure times are arbitrary beside exposure must be
the same for both images in every pair. Mean values of pairs
should cover the whole sensor dynamic range.
Calculation could be limited e.g. to an equally illuminated
area (sub-frame). Such sub-frame can be defined using count-box
controls, or area can be framed on any image, opened from set, and
the tool takes this area as sub-frame dimensions.
Calculation of Read Noise requires presence of a pair
with zero exposure time (bias frames).
Full Well Capacity is calculated correctly only if a
pair of images with higher mean value (longer exposure time) is
fully saturated. However, even if such pair is not present in the
set, the maximal ADU value for saturation can be entered manually
(4095 for 12-bit cameras, 65535 for 16-bit cameras etc.) to
calculate proper Full Well capacity.
Warning: Please keep on mind the sensor characteristics are
calculated using statistical analysis, and thus results may
slightly vary depending on the set of test images, their dynamic
range, sub-frame selected for analysis etc.
Bug fixes
The most important bug fix concerns Guider tool window. SIPS
v3.20.2 contained new code, despite the new functionality is not
yet accessible to users in current SIPS versions, which caused
program could fail when trying to guide. New version 3.21 fixes
this issue.
SIPS is a freeware and can be downloaded from the Download section of this web site.
Do you want to stay informed about new SIPS versions and features?
Follow @sipssw
on Twitter.
|